One of AB Serve’s purposes is to assist its customers with their quality’s and industrial logistics’ issues. The dedicated teams of experts endeavor to find and to set up reliable and sustainable custom-made solutions, which become integrated into the process of continuous improvement of the company.
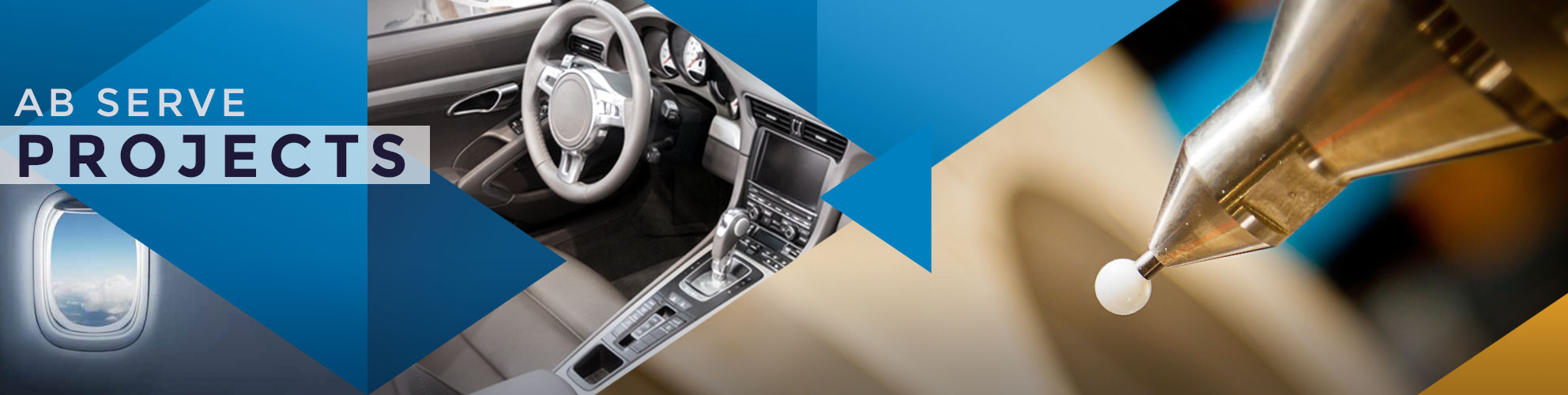
Who better than logisticians to manage your logistics?
While everyone agrees that logistics is a logistics business, many entrepreneurs are reluctant to outsource it for fear of losing control of operations. Accompanied by AB Serve, the manager of this factory has taken the plunge. Its experience proves it: there is no better than logisticians to manage logistic problems!
“Entrust a service provider or not?” “Continue to devote a lot of time and energy to the management of internal logistics, to the detriment of business development, or entrust it to a logistics expert, of course, but who knows my business as well as I do?” To remove the doubts of its customer, AB Serve offers a test over a quarter, a kind of trial period.
The customer accepts and entrusts the management of all the physical and IT flows of the plant to AB Serve. Through this mission, which includes:
– loading / unloading of trucks,
– inspection upon receipt of supplier deliveries (quantity, transport damage, reference checks),
– tidying up and storing goods,
– management of empty packaging,
– data entry and computer monitoring of stocks,
– the deconditioning and reconditioning of parts,
– supply of production lines,
The customer expects his service provider to manage from A to Z, in order to be able to refocus on his core business.
The AB Serve logistics manager begins by building up his teams. One for each of the plant’s stations. He ensures that the human resources and the material are perfectly adapted. At the same time, he informs the customer of the areas for improvement that he detects within the plant, and, upon approval, makes some adjustments to the installations to optimize flows. The preliminary phase is finished, the mission can be launched.
The three-month review is final! This well-established method has indeed freed the customer from all constraints related to the logistics of his plant, but not only …
The following were observed during this test trimester:
a significant reduction in turnover and absenteeism within logistics teams,
a reduction in incidents related to inventory management and line supply,
a reduction in material incidents.
Productivity gains estimated at 17%!
These results can be explained in particular by:
– optimization of staff and human resources,
– optimization of the choice of equipment, and the AB Serve / Fenwick partnership which guarantees optimal responsiveness for maintenance or replacement of equipment in the event of technical failure,
– optimization of physical flows (by redeveloping certain areas).
