One of AB Serve’s purposes is to assist its customers with their quality’s and industrial logistics’ issues. The dedicated teams of experts endeavor to find and to set up reliable and sustainable custom-made solutions, which become integrated into the process of continuous improvement of the company.
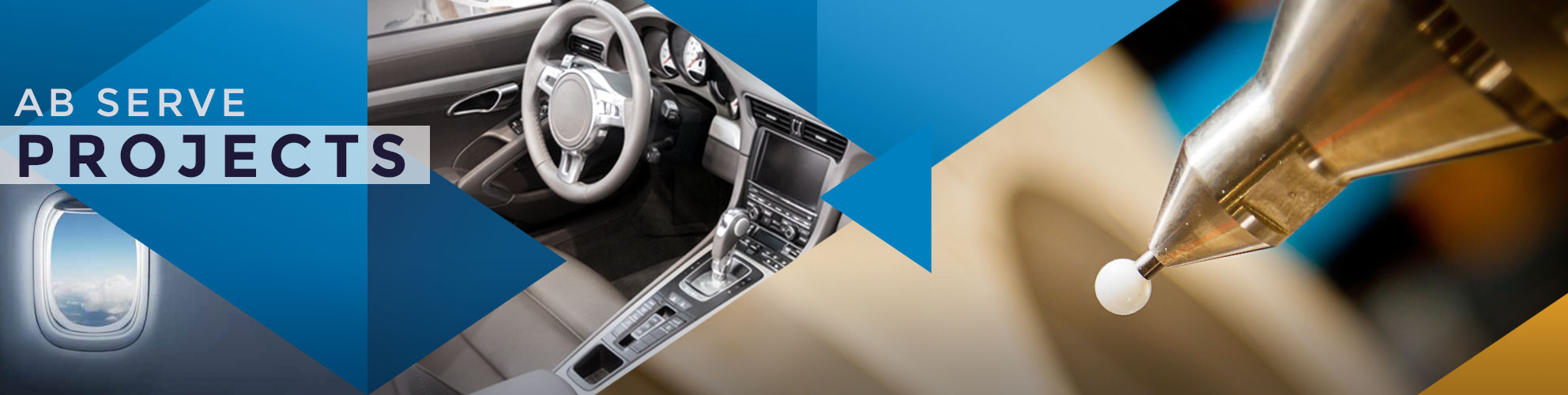
Mission to Russia
In charge of putting an end to the too many customer complaints, using their expertise within quality and organization fields, AB Serve assigned one of its consultants at a Russian original equipment manufacturer’s. The targets set by both the group and the client had to be met within 7 weeks.
Just a few months after its Russian subsidiary company’s opening, an international group producing plastic parts called upon AB Serve within the scope of a difficult start-up – tight schedule, brand new teams and brand new plant had indeed all been sources of dysfunctions.
Through a KAIZEN approach, the expert implemented a number of European quality and management standards, and trained on-site production, quality and management teams. Only three weeks after the start of the operation, his measures had straightened the situation: no more defects among any deliveries nor any customer complaints no longer occurred, and customer’s audits were successful.
AB Serve made use of the four following weeks to stabilize the output and support the continuous improvement process.

